Der digitale Zwilling zählt als eines der Buzzwords im Bereich Industrie 4.0, aber was steckt dahinter und wie kann eine Umsetzung erfolgen?
Der Begriff digitaler Zwilling bezeichnet ein Modell, das mithilfe von Computertechnologie die Verbindung zwischen der realen und virtuellen Welt herstellt. Das Hauptziel besteht darin, Verbesserungen in der realen Welt zu erzielen. Dabei werden reale Objekte, Prozesse oder Dienstleistungen in digitale Repräsentationen umgewandelt und in einer bestimmten Frequenz und Genauigkeit miteinander synchronisiert. Dies ermöglicht eine enge Interaktion zwischen der physischen und virtuellen Welt zur Steigerung der Ergebnisse und Effizienz.[1]
Einfache Beispiele zur Umsetzung und Veranschaulichung sind jedoch eher beschränkt. Aus diesem Grund ist die Idee eines Demonstrators entstanden, der mit möglichst einfachen Mitteln die Vorteile eines digitalen Zwillings und der Simulation insbesondere für KMUs näherbringen soll.
Aufbau und Kopplung der physischen Anlage mit dem digitalen Modell
Die Abbildung 1 zeigt den prinzipiellen Aufbau des Demonstrators, der sich aus folgenden Komponenten zusammensetzt:
- Fischertechnik-Modell als physische Anlage
- speicherprogrammierbare Steuerung (SPS, Siemens Simatik S7-1500) mit integriertem OPC UA[2] Server
- Digitales Modell entwickelt mit der Software Tecnomatix Plant Simulation
- Webbasierte grafische Benutzeroberfläche entwickelt mit Node-RED
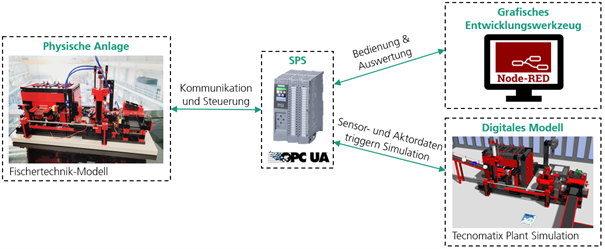
Abbildung 1: Aufbau des Demonstrators
Im Rahmen des Projekts wird ein Fischertechnik-Modell verwendet, welches einen kleinen Produktionsprozess demonstriert. Die Produktion startet mit einem Brennprozess im Ofen, der durch eine Meldeleuchte symbolisiert wird. Anschließend wird das Bauteil über einen Vakuumgreifer zum Drehteller transportiert, der das Bauteil zur Fräse bringt. Nach dem Fräsprozess wird das Bauteil durch den Drehteller auf das Förderband transportiert. Der Prozess endet am Förderband mit dem Durchqueren einer Lichtschranke. Die Steuerung des Fischertechnik-Modells erfolgt über eine Siemens SPS, die auch in der Industrie für Steuerungsaufgaben im Maschinen- und Anlagenbau verwendet wird. In der SPS werden die Sensoren und Aktoren entsprechend ausgewertet.
Basierend auf dem Fischertechnik-Modell wurde mithilfe der Software Tecnomatix Plant Simulation ein digitales Modell erstellt. Die Kopplung der physischen Anlage mit dem Simulationsmodell erfolgt über die OPC UA Schnittstelle, indem die Sensor- und Aktordaten das digitale Modell triggern. Durch diese Kopplung wird eine Synchronisation zwischen physischen und digitalen Abläufen erreicht. Das bedeutet, dass die Bewegungen und Aktivitäten des Fischertechnikmodells mit dem digitalen Modell abgeglichen werden. Dadurch folgt das digitale Anlagenmodell dem realen Modell nahezu in Echtzeit. Über die webbasierte, grafische Benutzeroberfläche können zudem verschiedene Anlagenzustände gesteuert werden wie z. B. die Einstellung der Brennzeit an der physischen Anlage. Auch hier erfolgt die Übertragung über die OPC UA Schnittstelle. In den folgenden Videos ist der physische und digitale Ablauf zu sehen.
Vorteile und Nutzen
Insgesamt ermöglicht die Kopplung des Fischertechnik-Modells mit der Simulationssoftware eine engere Verknüpfung zwischen der realen und digitalen Welt und bietet je nach Anwendungsfall und Planungsvorhaben viele Vorteile, Beispiele dafür sind:
- Optimierung der Produktion und Logistik
- Energieeinsparung
- Fehlerreduzierung
- Zeiteinsparung in der Inbetriebnahme
- Absicherung von Planungsszenarien
- Visualisierung
- Was-wäre-wenn-Szenarioanalysen
Insbesondere in Hinblick auf energetische Aspekte, können durch die Anreicherung des Simulationsmodells mit Energiedaten energetische Betrachtungen durchgeführt werden, ohne eine durchgängige Leistungsmessung an der physischen Anlage vornehmen zu müssen. Dadurch können Abschätzungen zu Energieeffizienz und Energieflexibilität getroffen werden, wie z. B. die Entwicklung von passenden Strategien zur Optimierung des Lastgangs.
Einsatz bei den Energy Open Days am Fraunhofer IWU
Der entwickelte Demonstrator wurde zum ersten Mal in der Veranstaltungsreihe »Fraunhofer IWU Open House« eingesetzt. Bei diesem neuen Format tritt das Institut in einen Austausch mit Partnern, Kunden und einer interessierten Öffentlichkeit – jedes Jahr zu einem aktuellen Thema. Neben Fachvorträgen und Expertenrunden boten die »Energy Days« vom 13. bis 15. Juni in Chemnitz auch vielfältige Einblicke in die Arbeit der Forschenden am IWU.
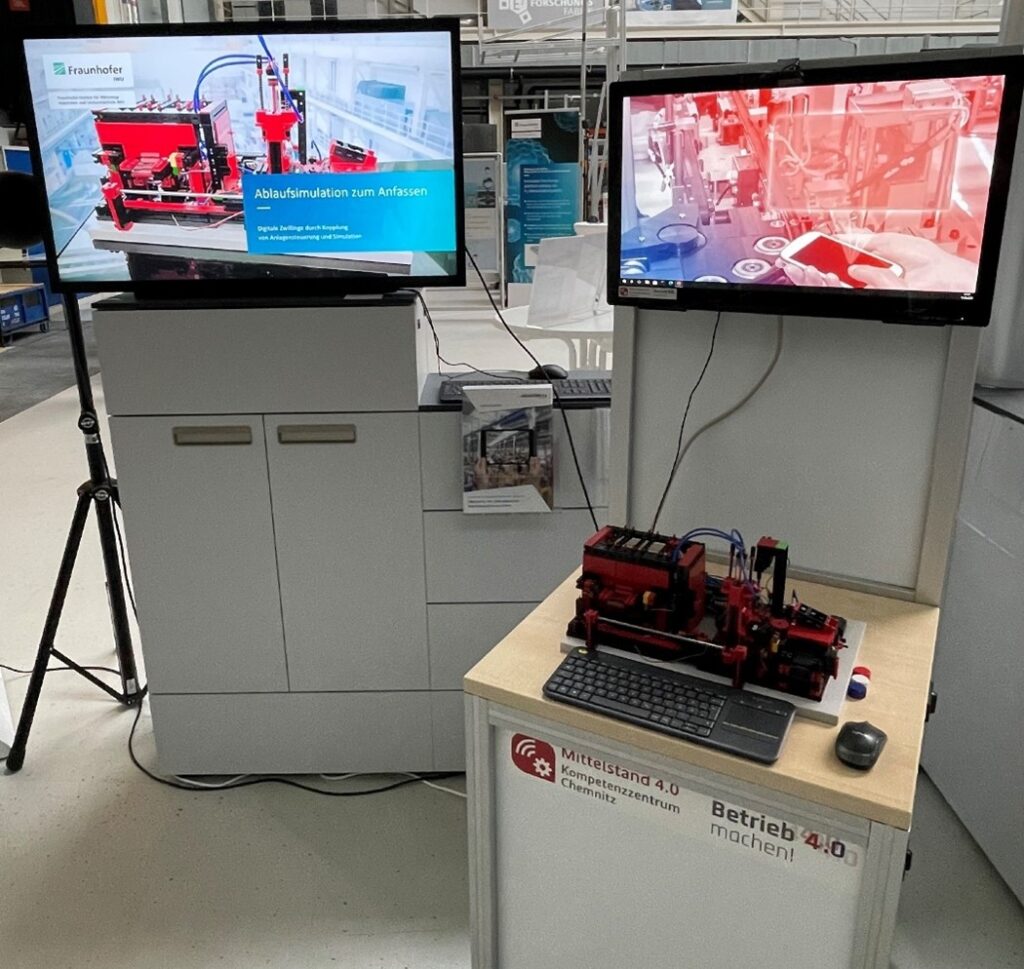
Abbildung 2: Einsatz des Demonstrators bei den Energy Open Days
Wenn Sie neugierig geworden sind und mehr über den Demonstrator und unsere Angebote erfahren möchten, kommen Sie gern auf uns zu. Weitere Beiträge zu diesem Thema finden Sie zudem auf dem Blog unter der Rubrik Simulation.
[1] Vgl. Olcott, S. und Mullen, C.: Digital Twin Consortium Defines Digital Twin, 2020. URL: https://blog.digitaltwinconsortium.org/2020/12/digital-twin-consortium-defines-digital-twin.html [Stand: 27.06.2023].
[2] OPC UA (Open Platform Communications Unified Architecture) ist ein industrielles und herstellerunabhängiges Kommunikationsprotokoll für den Informationsaustausch zwischen Produkten unterschiedlicher Hersteller. (https://opcfoundation.org/)
Kommentare hinzufügen